View previous topic :: View next topic |
Author |
Message |
Lagondanet Administrator

Joined: 03 Jan 2007 Posts: 3110 Location: UK
|
Posted: Tue Mar 05, 2013 7:51 pm Post subject: |
|
|
Great job Jonathan especially for a first attempt and well described.
Rather you than me. I can only look on in awe. |
|
Back to top |
|
 |
Vrije
Joined: 23 Nov 2007 Posts: 440
|
Posted: Tue Mar 05, 2013 8:24 pm Post subject: |
|
|
Cool work Jonathan, but in case you (anybody else) would stick to the original rubber diaphragm/sheet, it is a bone stock part being used by lots.
From Saab to Land rover, all the same measurements
At work I do ocasionally replace them (some once a month)
Can't find them new ? go for a (any)passenger side seat but I'd go for
a Landy Discovery and break them(even cut them if you will) ,they're like new! will take just a few minutes. Succes
harry |
|
Back to top |
|
 |
jonc
Joined: 21 Sep 2010 Posts: 584 Location: Cheshire, UK
|
Posted: Sat Apr 13, 2013 9:25 am Post subject: |
|
|
Thanks Harry and Roger for your comments.
Now I have the colour restoration completed on the few pieces. I wanted to do the absolute minimum restoration work to the leather because the finish is never the same when it is done and takes a long time to get back the original grain. I have learnt that this is because originally, the when the leather was coloured ('Connollised') it then went through a process which stretched/crushed/pummelled it at Connolly to give it the finish we expect before it is turned into our interior by the AML trim shop. After re-connollising (which is basically a multi-layer spray-painting process) the leather is smoother. Over time and with use it gets back its patina. Until this happens, it is also a dirt-magnet since the finish starts off more rough than the original. I found this when I had the Spirit interior restored.
Having said all that, the work was done by ex-Connolly staff - people that the franchise dealers and restorers of the North use.
The other reason for doing as little restoration as possible was that the leather of the car is actually in really great shape.
Here is the drivers seat going back together:
The two pieces were restored separately, and then they bolt back together at the back edges of the base. Here is when I took it apart:
Once they are bolted together, the leather of the base can be finished off. The head rest also needs refitting. It is slotted into place and secured with two split pins so it lives permanently in the seat back normally:
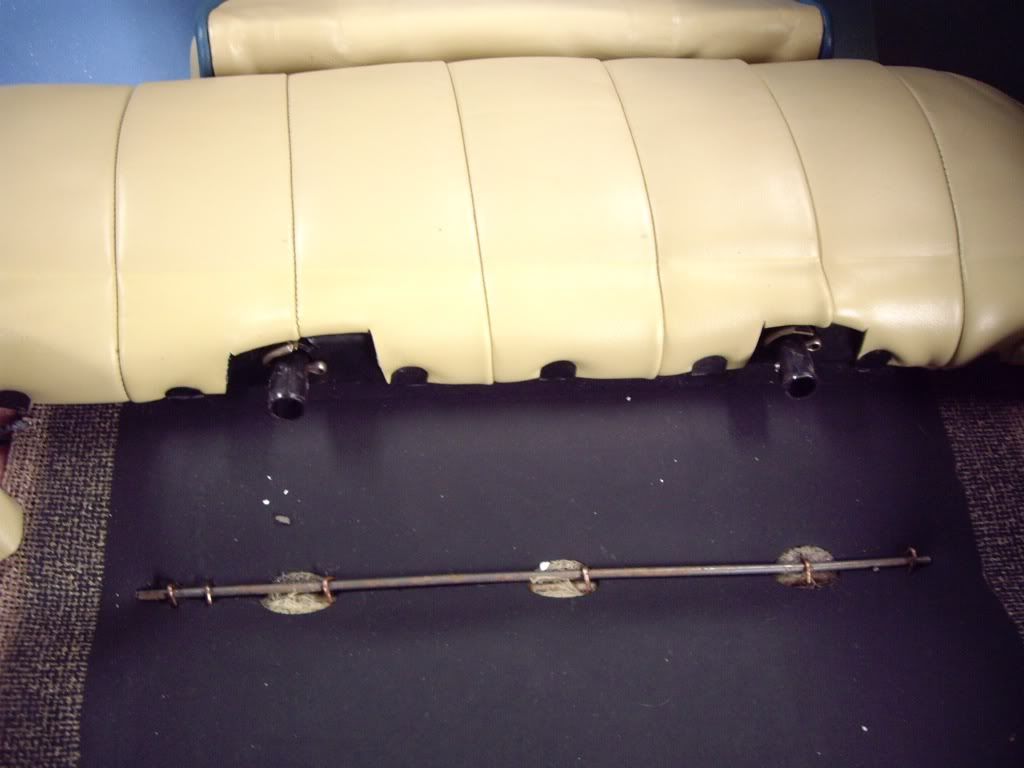 |
|
Back to top |
|
 |
jonc
Joined: 21 Sep 2010 Posts: 584 Location: Cheshire, UK
|
Posted: Sat Apr 13, 2013 9:30 am Post subject: |
|
|
The motor for reclining the seat lives in the seat back and so its cable needs putting back in place. It comes out of the seat through a hole in the diaphragm in the base. I used a wire to pull it through into position:
After refitting the seat chassis which deals with the height and forwards-backwards, the leather trim under it on the floor needed a good clean. This was also the time to clean and feed the leather of the hand brake:
Seat now back in the car. The rest of the interior is not finished, but the seat needed to go in so I could get the car to a stainless-steel exhaust specialist to deal with the crack in the left manifold.
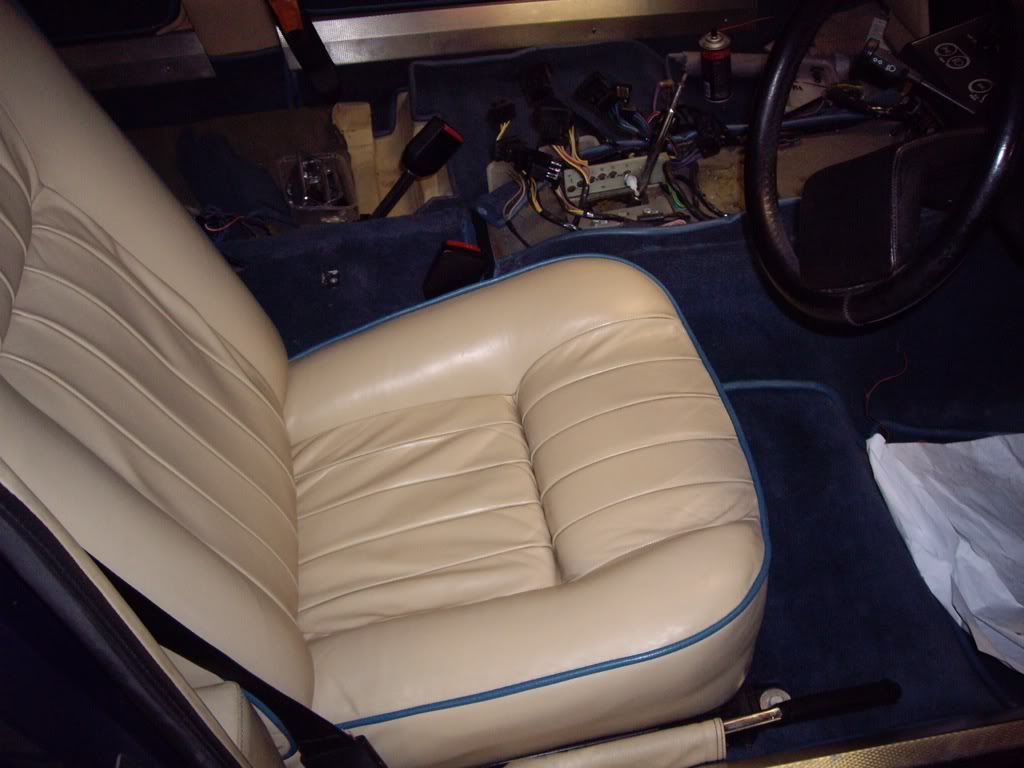 |
|
Back to top |
|
 |
jonc
Joined: 21 Sep 2010 Posts: 584 Location: Cheshire, UK
|
Posted: Sat Apr 13, 2013 9:36 am Post subject: |
|
|
So.. the car went into the specialist before I went on holiday, so it could be sorted while I was away. Here is the problem:
However, the manifold is in a worse state than I had anticipated. It could probably be welded, but would be unlikely to last, and in any case, the flanges are down to about half their original thickness:
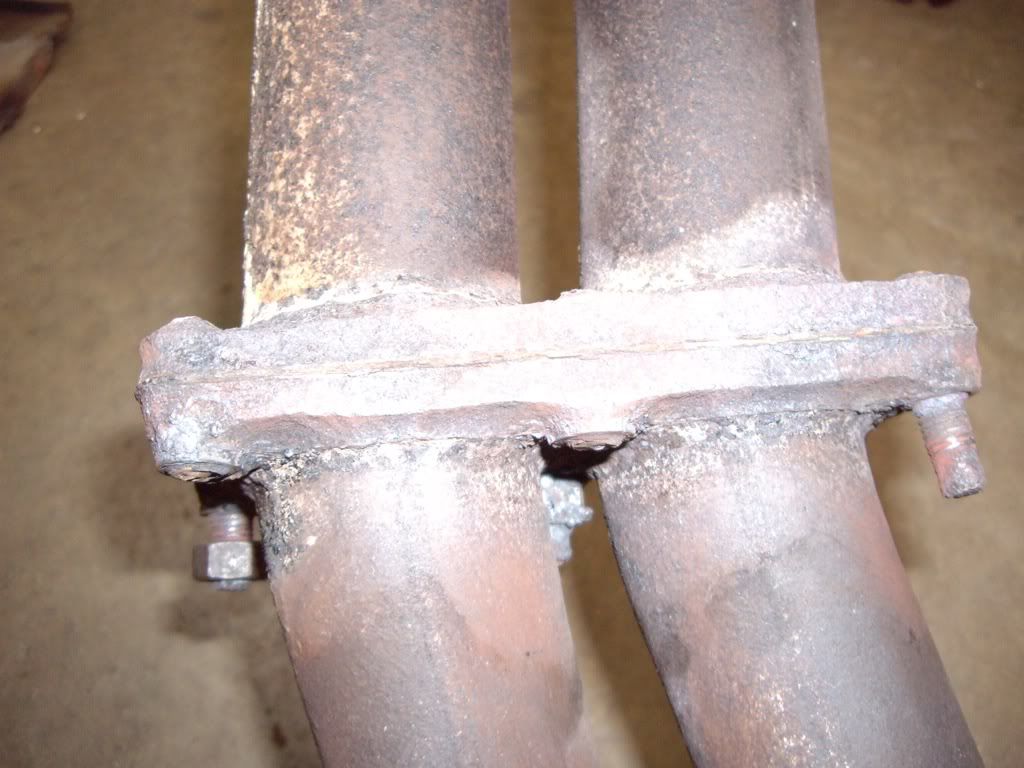 |
|
Back to top |
|
 |
jonc
Joined: 21 Sep 2010 Posts: 584 Location: Cheshire, UK
|
Posted: Sat Apr 13, 2013 9:39 am Post subject: |
|
|
So, a replacement was obtained from AML - the last one in stock:
Its a real beauty:
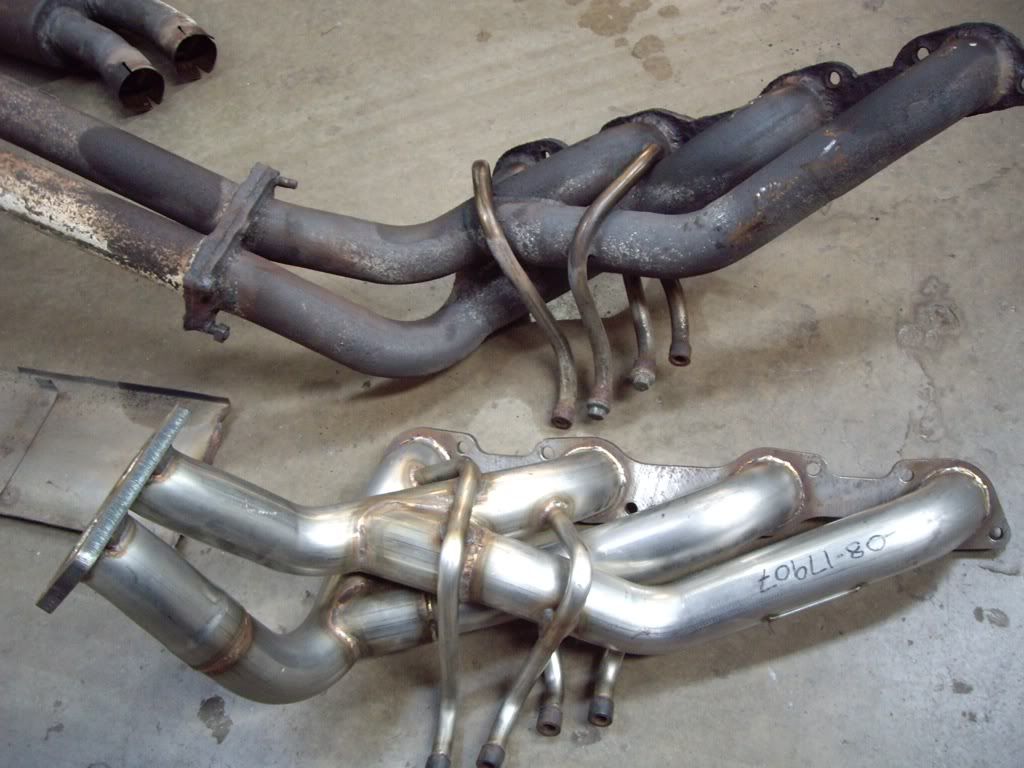 |
|
Back to top |
|
 |
jonc
Joined: 21 Sep 2010 Posts: 584 Location: Cheshire, UK
|
Posted: Sat Apr 13, 2013 10:32 am Post subject: |
|
|
..in fact, it is better made than the original one.
There are some slight differences - the flanges are slightly thicker and every other tube has a sleeved joint. I suspect this design change was more to ease assembly than anything else but it will likely be stronger, particularly in the areas prone to cracking.
The test-port tubes are also different - the bends are fixed-radius and they are better welded in place. It also has a manufacturer's plate on it:
Unfortunately, AML didn't have the right one which I would have bought as well. They also said they could give no indication of when they would be able to supply one.
The manifold pipes have compound bends in them - something you can only produce on a computer-controlled automatic bending machine. You can't create the same thing manually as each bend is separately welded together.
I tried to track down the manufacturer. CLF were the OEM supplier to Aston, Bentley, Jaguar etc but folded in 2008. The assets were bought by Unipart but I spoke to someone in the same industry and the same area as CLF who suggested the patterns/program would be long gone. So - likely a dead end.
I am having one hand-made to as close a copy as possible. First step is to laser-cut the flanges and at the same time they are laser-cutting a new set of heat shields for the down-pipes which I am replacing.
I will also be making the set of test-pipes and so need to make the ends which the brass plugs screw into. Luckily, I recently acquired a lathe.. |
|
Back to top |
|
 |
Lagondanet Administrator

Joined: 03 Jan 2007 Posts: 3110 Location: UK
|
Posted: Sun Apr 14, 2013 9:43 pm Post subject: |
|
|
Excellent! What more can I say? |
|
Back to top |
|
 |
jonc
Joined: 21 Sep 2010 Posts: 584 Location: Cheshire, UK
|
Posted: Wed Apr 24, 2013 10:30 am Post subject: |
|
|
Manifold is nearing completion. It is being made to resemble and match the new one as close as possible, so has sleeved joints in a couple of places:
Again, it is better made than the original. This manifold has to clear the steering column and so is not symmetrical to the left side. There is a particularly nasty bend on the original which is much nicer on the replacement:
It just needs a set of test pipes fitting so it is now with another company who are making them and then I can get them welded on. |
|
Back to top |
|
 |
Christoph
Joined: 19 Feb 2011 Posts: 51
|
Posted: Fri Apr 26, 2013 9:56 pm Post subject: |
|
|
Jonathan you are a real artist. Have you made it with your new lathe?
THIS IS GREAT! I might come back to this. _________________ Christoph |
|
Back to top |
|
 |
jonc
Joined: 21 Sep 2010 Posts: 584 Location: Cheshire, UK
|
Posted: Sat Apr 27, 2013 8:06 am Post subject: |
|
|
Hi Christoph,
I agree it is real craftsman work, but I didn't make it! My oxy-acetylene welding is that good, but I have never TIG welded.
It was made by a very talented man at TopGear Stockport, makers of the Longlife stainless steel systems. http://www.topgearstockport.co.uk/
The test pipes were bent from 12mm stainless on Friday by another local company - Atlas Tube Bending in Oldham, but all I am making is the ends for these, which will be welded to the end of the test pipes.
Jonathan |
|
Back to top |
|
 |
jonc
Joined: 21 Sep 2010 Posts: 584 Location: Cheshire, UK
|
Posted: Wed May 01, 2013 8:07 pm Post subject: |
|
|
So, I am making the ends for the test pipes. They are 16mm diameter with an M10 thread in side them which the brass screw fits into. Although the exhaust tubes are stainless steel, these are made of mild steel. This is because it is far easier to machine than stainless, and they don't rust in this location due to the heat keeping them dry.
I bought some 16mm steel bar which first has a flat end machined with a chamfer on the outside edge, then has to be drilled out to 8.5mm ready for threading.
Next, I tapped the hole. I did this to beyond the depth needed for each piece.
Finally, the piece is cut from the end of the bar. This is done with a thin parting tool:
And here is the end result:
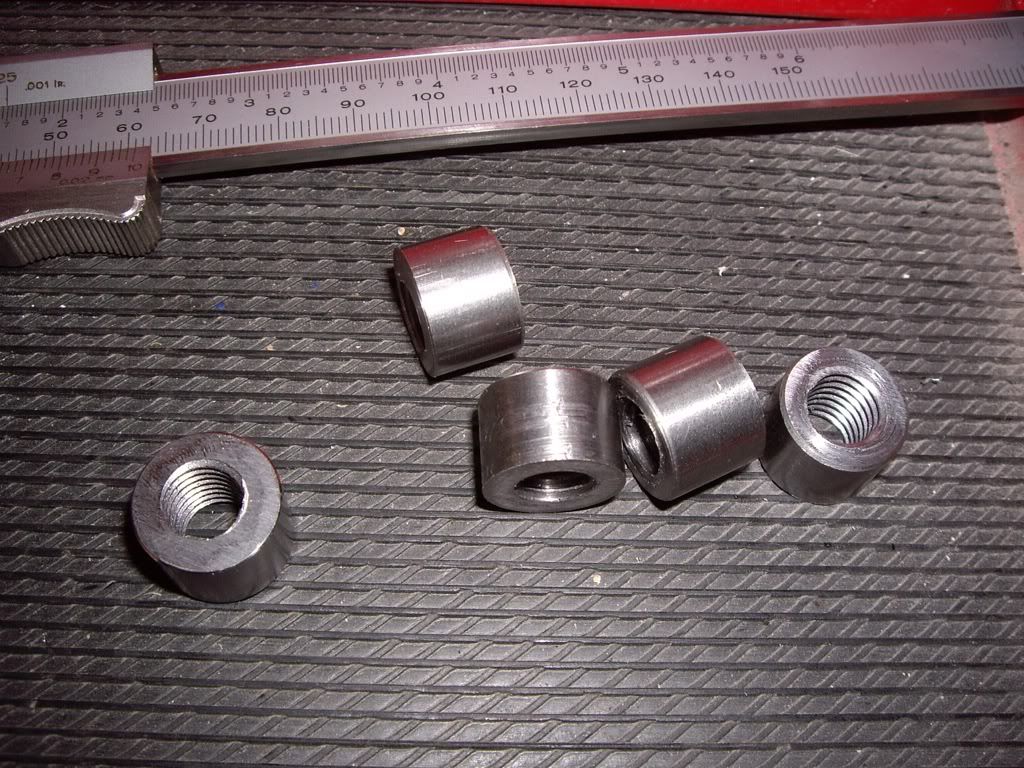 |
|
Back to top |
|
 |
jonc
Joined: 21 Sep 2010 Posts: 584 Location: Cheshire, UK
|
Posted: Wed May 01, 2013 8:17 pm Post subject: |
|
|
And here they are on the car:
They have new brass plugs from AML fitted and the manifolds are back on the car.
Next will be the downpipes, which are new too:
They are getting new heat stainless steel heat shields which fit above them and so are being welded into place when they are on the car.
The rest of the system is scrubbing up nicely.
Before:
After:
Before:
After:
Hopefully all back on the car this week (fingers crossed). |
|
Back to top |
|
 |
Lagondanet Administrator

Joined: 03 Jan 2007 Posts: 3110 Location: UK
|
Posted: Wed May 01, 2013 9:29 pm Post subject: |
|
|
Looking very good!
 |
|
Back to top |
|
 |
jonc
Joined: 21 Sep 2010 Posts: 584 Location: Cheshire, UK
|
Posted: Fri Mar 13, 2015 8:17 pm Post subject: |
|
|
I never did get round to finishing off posting about this. Some catching up to do..
Here is the exhaust system back on the car:
You may notice that all the clamps are new, stainless steel ones which are much better than the original steel U bolt ones. |
|
Back to top |
|
 |
|